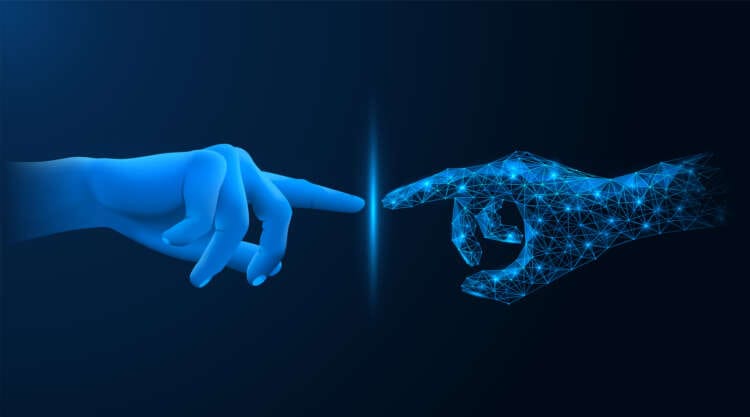
Cobots are becoming increasingly popular in most production processes. Their human interaction and ability to regulate their force around humans make them particularly special. Understanding the basics of donors and how they work is crucial to the effective working of robots.
What Is A Cobot?
Cobots are collaborative robots. They are a lot like the traditional industrial robots but have a lot of upgrades that make them safe to work in the same environment as humans. As they gain popularity, they are quickly replacing traditional robots.
Most cobots can work on multiple axes. They have a shape or form of a lightweight arm or double arm.
Cobots have several uses, including;
- They are at the front lines of assembly lines. Cobots can pick up and move items.
- Cobots are suitable for packaging jobs at the end of an assembly or production line.
Even though cobots are typically safe and interact well with humans, a typical cobot would need to work under the supervision of an operator. It is to ensure that all cobot systems are functioning correctly. Operators are also on standby to deal with any potential failures in the cobot systems.
One of the ways that cobots can interact well and safely with humans is because of the safety tools installed in the cobot. Some of these tools include;
Cameras: These can be 2D or 3D cameras that enable the cobot to see what is in its surroundings. Even though the cameras help the cobot perform tasks more efficiently, they can also detect humans around and stop if they get too close.
Sensors: Many different types of sensors respond to other stimuli. Depending on the triggers, such as motion, heat, etc., the sensors will detect human operators if they are too close and stop automatically.
Cobots are remarkable because they can handle incredible amounts of weight. The majority can deal with between 5 and 100 kg. Some cobots in specific sectors, such as aeronautics, can lift approximately 300 kilograms.
Other safety measures include the cobot automatically stopping if they have trouble or resistance to moving an arm. They also tend to move slowly to accommodate the humans working within the same environment.
Testing a cobot is simple. A simple tap on the robot arm is enough for most cobots to start or stop it.
How To Choose A Cobot For Your Company
Many factors determine whether a company should invest in a collaborative universal robot or not. Investors should think carefully about their why before choosing when to invest and which cobot best serves their needs.
Have A Clear Understanding Of Your Company’s Needs
Cobots may be excellent and practical tools, but there needs to be an excellent reason to invest in them. Knowing the why will determine what type of cobotto choose. Here are a few reasons to invest in cobots;
- Workload – Opting for cobots is a great idea when a company needs to scale or increase production and is seriously understaffed. A single cobot can perform several tasks at a time.
- Automation – It is a huge deal in many manufacturing companies. It is efficient and fast. Human workers aren’t tasked with repetitive tasks for several hours each day when using automated processes. Instead, they can be involved in supervision, making sure operations are running smoothly.
- Improved Working Conditions – Most jobs in production companies are dangerous. Even with safety measures, workers can still face some risky situations. Incorporating a cobot can be helpful because it can perform more complex tasks. They are also great replacements for industrial robots, which are dangerous for humans to work around.
- Savings – Robots are a significant investment because they help companies save on extra costs. Cobots are less prone to make mistakes which reduces wastage. Their efficiency and speed mean higher production levels in less time.
Cobots also generally take up less space than industrial robots meaning that companies can also save up on room used when they invest in cobots.
Resource Assessment
One factor that significantly affects whether to invest in a cobot and the specifics. These are greatly determined by the resources available.
- Budget
Cobots are much cheaper than traditional industrial robots. Regardless, cobots aren’t cheap either. Companies investing in cobots need to ensure they can afford them and any additional tools they may need to purchase, such as grippers and tool changers.
Some other costs include hiring experts to program and supervise the cobots. An alternative may be to train existing staff, but it requires time.
- Time
It’s important to consider how much time it would take to set up cobots in hardware and software and determine if the company has that much time.
Cobots work well with human workers, but the processes run smoothly only when the workers are equally fast. However, proper integration requires time. How much time is the company willing to spend?
- Space
Cobots are much smaller than industrial robots, which makes them advantageous. However, cobots have arms that move on an axis. Is there enough room for the cobot to run smoothly?
Traditional robots are usually motionless. They are drilled into the ground, and screws hold them in place.However,cobots can move around freely within a workstation. Consider whether there is enough room for the cobot to move in an assembly or production line.
- Expertise
Human interactions with collaborative robots are essential. Skilled workers need to handle the software, from the simulations to the actual implementation of the software into daily tasks.
Cobots work a bit slower than traditional robots to accommodate human workers. Even so, they are still relatively fast and efficient. Human workers need to be skilled enough to keep up with the pace of the cobot to keep processes working smoothly.
The workers also need training on expectedconduct around the robots to avoid injuries.
Wrapping Up
Incorporating cobots into daily tasks can be awkward and challenging at the beginning. Be patient and allow time for organic interactions between the collaborative robots and human workers.
This is a Sponsored Post